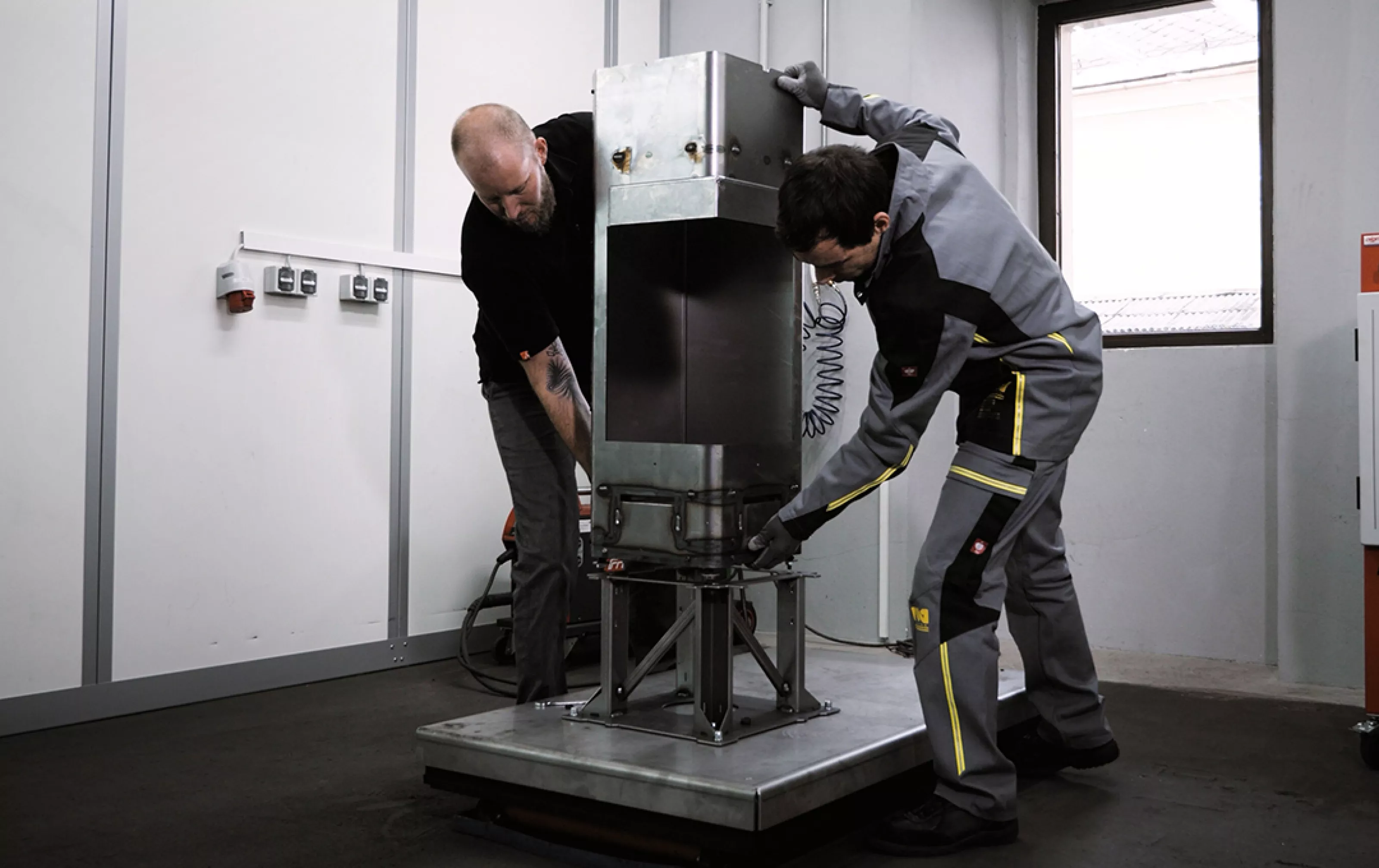
A stove is created: It all began with an idea
From the first sketch to the finished stove: The RIKA product development team offer a fascinating look behind the scenes.
RIKA is the European market leader in the pellet stove segment and one step ahead of the stove industry in many respects. The high value placed on technology and innovation is particularly evident in the in-house mapping of the entire product development process. Not only the in-house hardware and software department, but also the internal test laboratory in particular – one of the most modern on the market anywhere – provide a crucial advantage. A well-coordinated, experienced team of highly qualified employees from a wide range of disciplines works hand in hand – the perfect conditions for technological innovations at the highest level.
From the idea to the first draft
Every product development is based on needs – the needs of customers and partners clearly come first: problems are to be solved and boundaries redefined. In the first stage, the ideas are fleshed out together and the new development’s essential product features are defined. This results in an initial basic design concept: the technical design, combustion technology, dimensioning of the combustion chamber and selection and positioning of the individual components are defined.
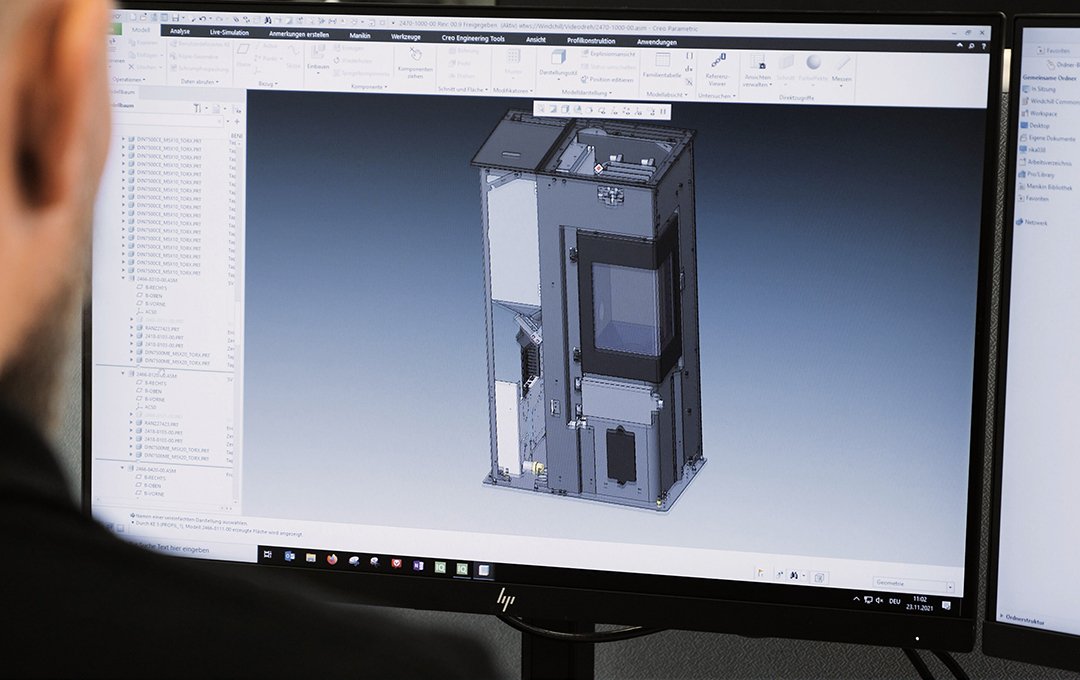
In the next stage, the basic concept is validated using computer-aided flow simulations and optimised step by step through geometric adjustments and the selection of suitable materials. The result is a heating sample draft.
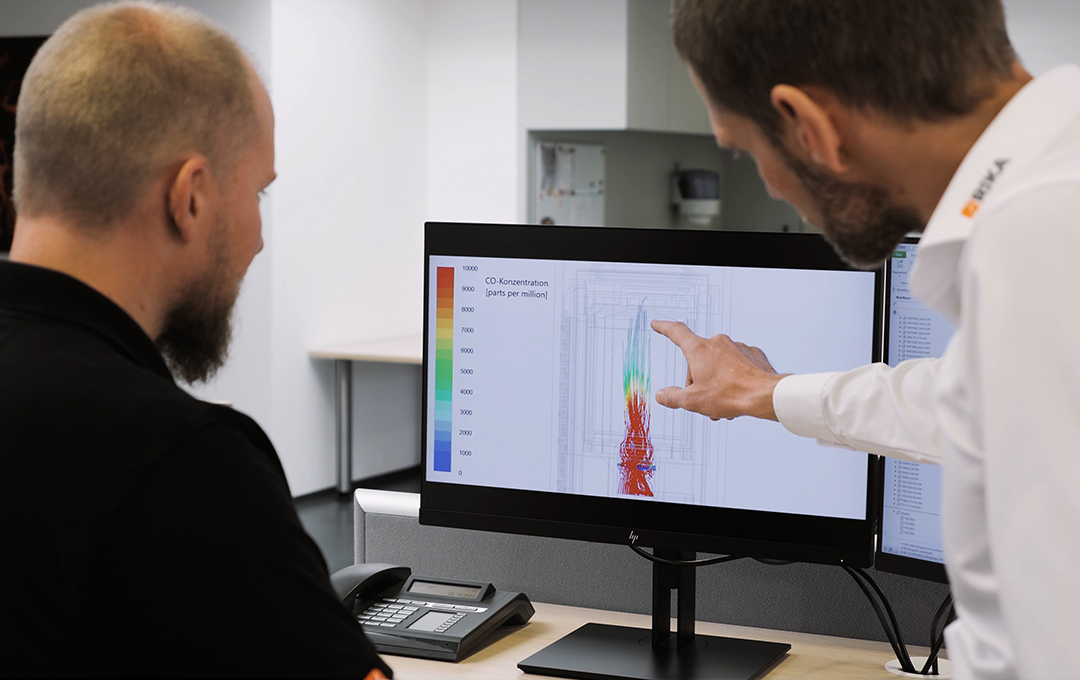
It’s all about the inner values: hardware and software
To ensure optimum combustion in the stove in the long term, tailor-made hardware is crucial, in addition to well thought-out mechanical design. The developers design all system-relevant assemblies using the latest CAD software. From component research and selection to the finished PCB layout, all areas are covered in-house. The hardware prototypes are also created on site. RIKA focuses on the highest component quality and safety.

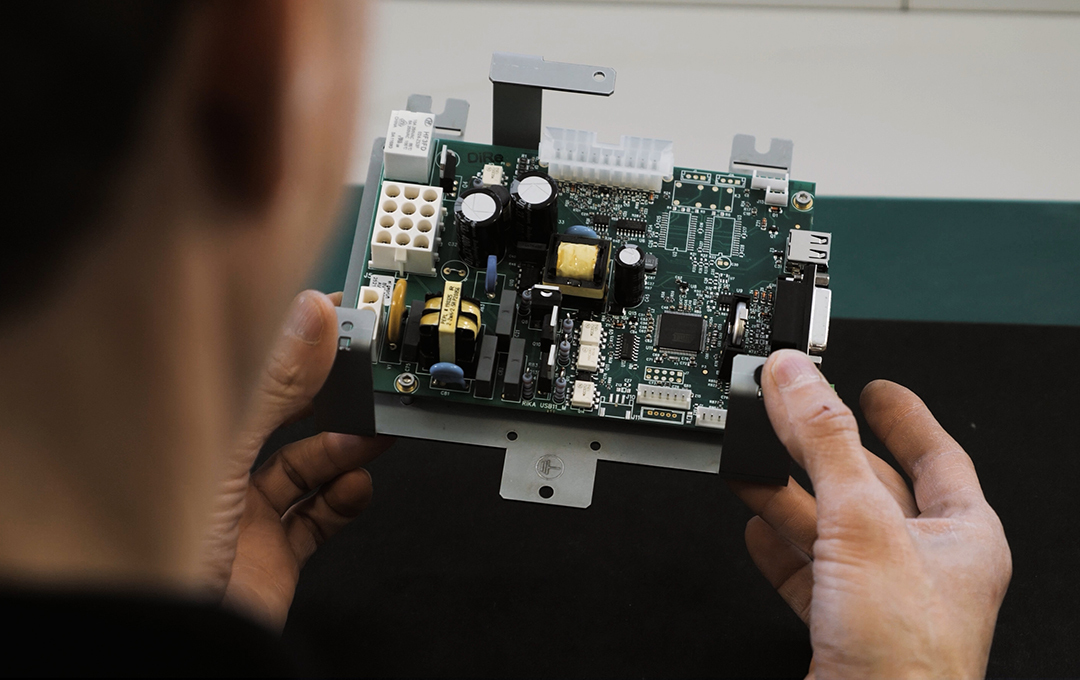
Now the software comes into play. The software developers program everything at RIKA: starting with reading sensor data to complex touch-display visualisation, wireless communication interfaces and even mobile applications for smartphones.
Handcrafted into a stove heating pattern
All individual parts are manufactured based on the design data. All sheet metal parts are manufactured in-house at RIKA and carefully assembled by hand. Great attention is already paid to the later series production during this phase. The design engineer assists with assembling the heating sample and incorporates suggestions for improvement directly into the design.
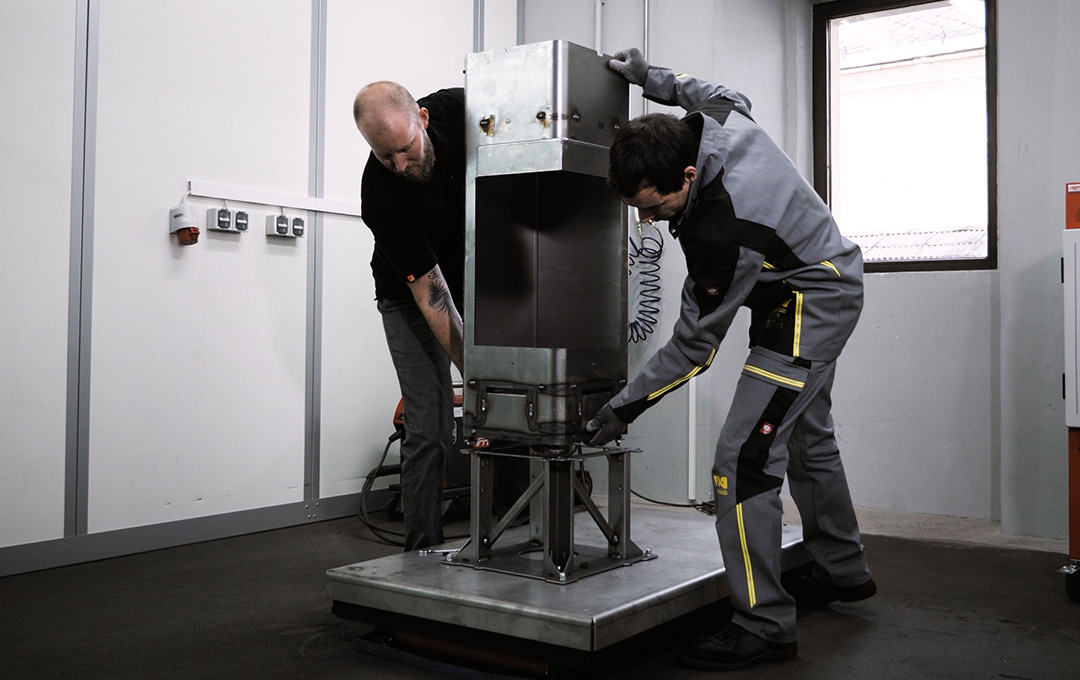
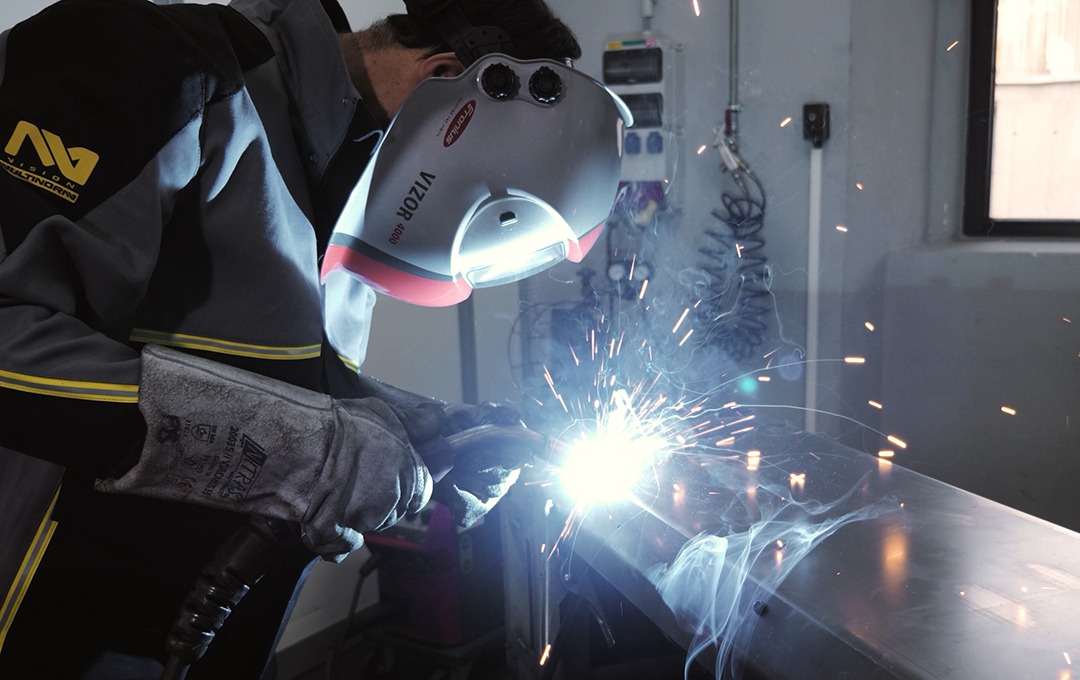
First test phase
In the test lab, ideas and visions are turned into tangible and measurable products for the first time. The stove heating sample is put through its paces using state-of-the-art equipment. The essential goals at this stage of development are, on the one hand, optimum combustion and, on the other, tight, safe operation. Although we also attach importance to user-friendliness and practical operation even at this stage.
Designing desire: the stove design
After the successful heating sample test, the design search begins together with the international design agency KISKA, a long-standing partner of RIKA. The aim is to find the perfect interplay between forms and functions as well as colours, materials and surfaces. The final concept is chosen from several design proposals together with management based on the aspects of appearance, feel and economic viability. In the next stage, the final design proposal is subjected to a rough technical feasibility check in the design department and then the manufacturing technology is worked out in detail.
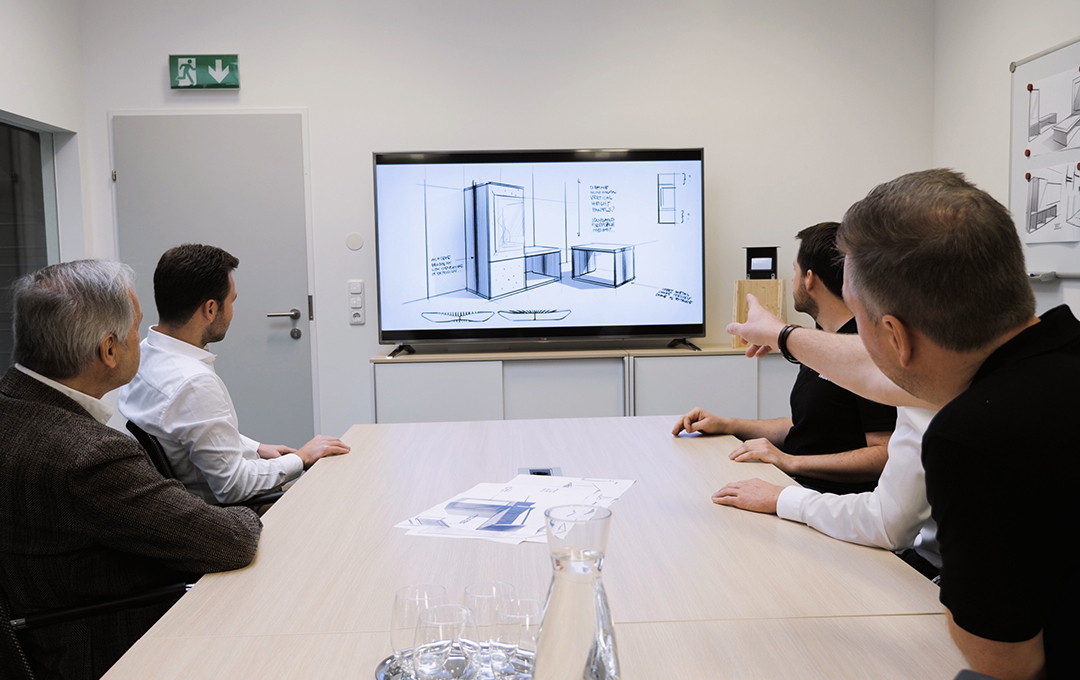
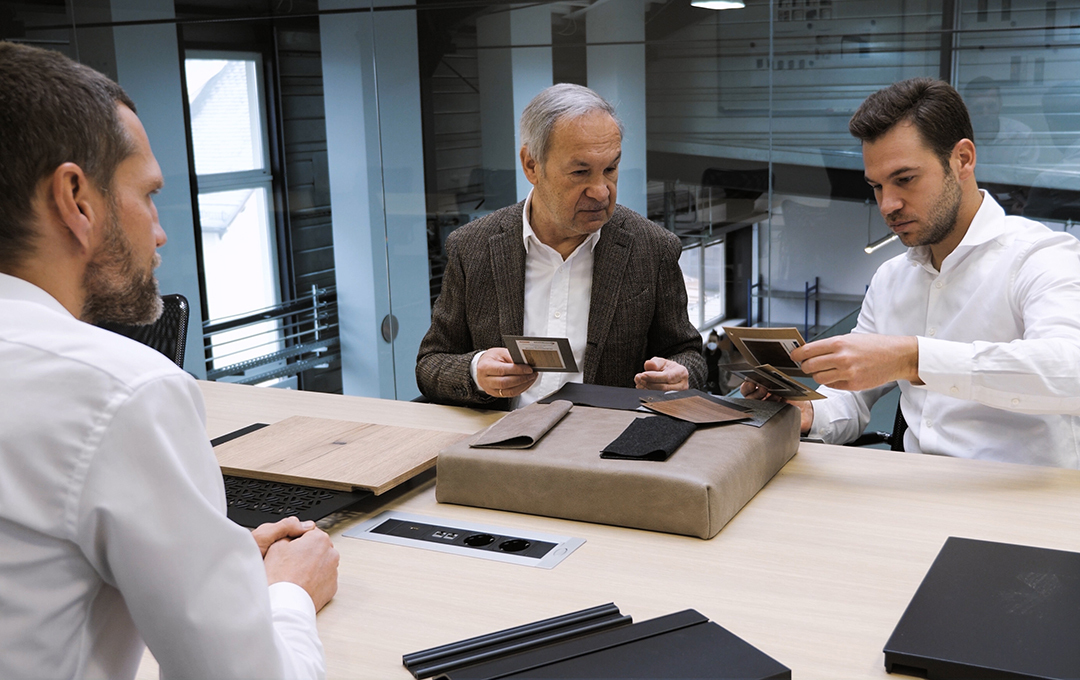
A first prototype is created...
The stove is finally assembled in prototype construction together with the designer, where ease of assembly and servicing as well as suitability for series production are the focus.
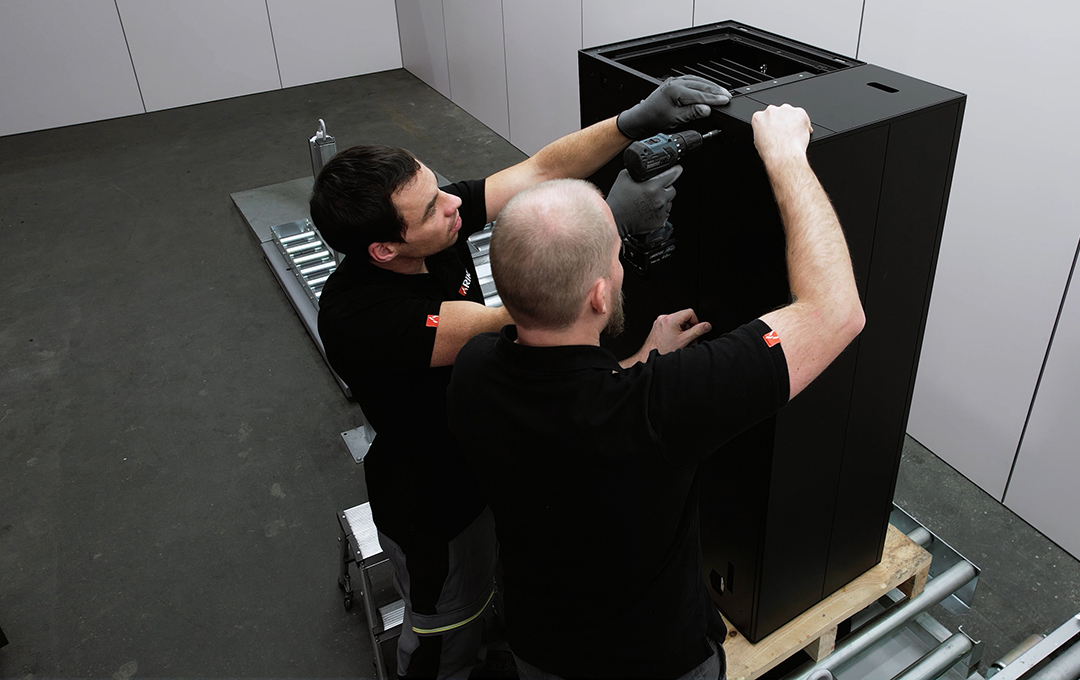
The first near-series prototype is subjected to extensive testing. The focus is clearly on verifying the design specifications. The safety-relevant standard specifications, such as temperatures in relation to adjacent components and materials, must comply with the standards. Likewise, emission values and efficiency must comply with the standard. In addition, usability, i.e. user-friendliness, is closely scrutinised in this phase. Together with the design and software development department, this is continuously developed further. The goal is a mature, technically flawless prototype, ready for type testing at an accredited test centre.
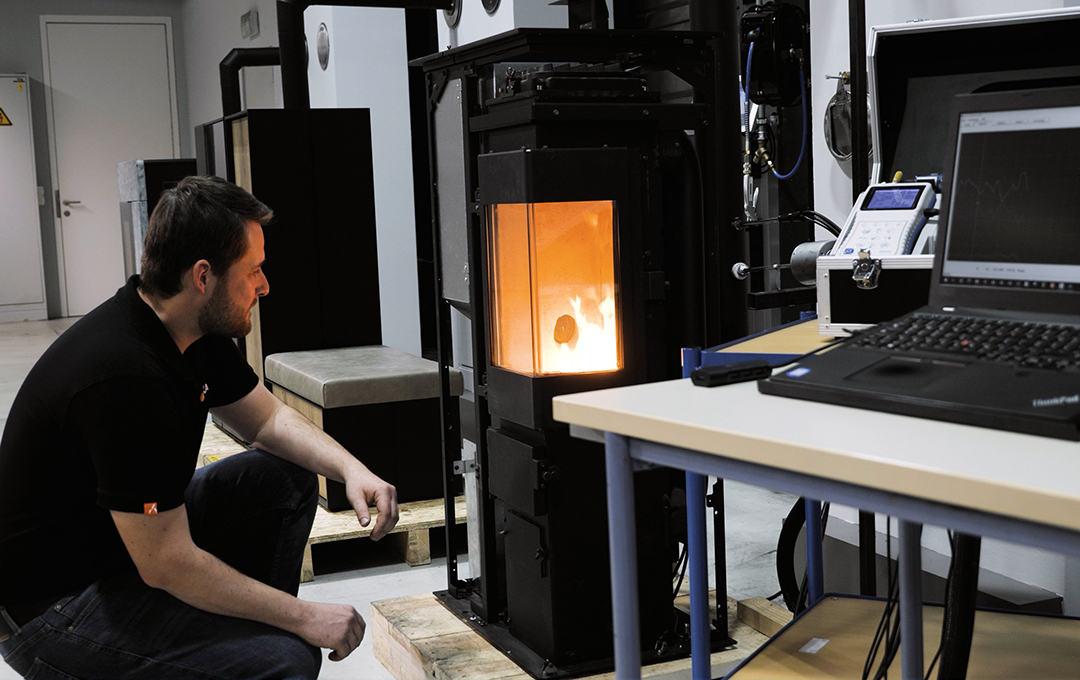
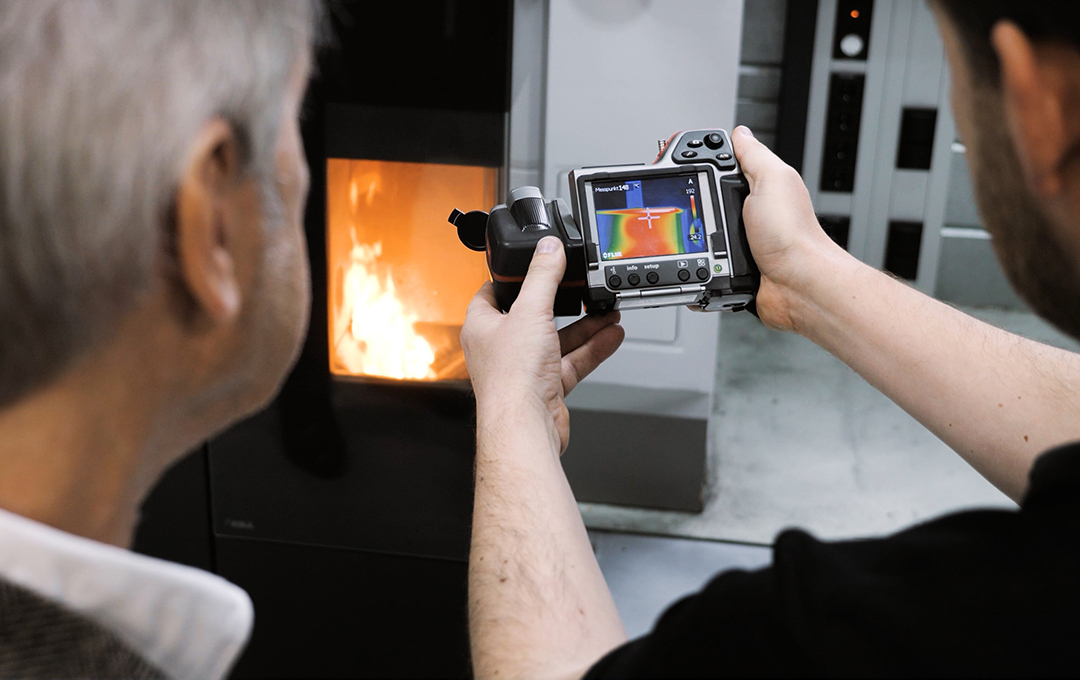
On the home straight: from pilot series to series production
The first ten appliances of the new stove model are produced in series production at the production site in Adlwang. After final testing in the test laboratory, series production is finally approved and the new stove model is added to the RIKA stove range.

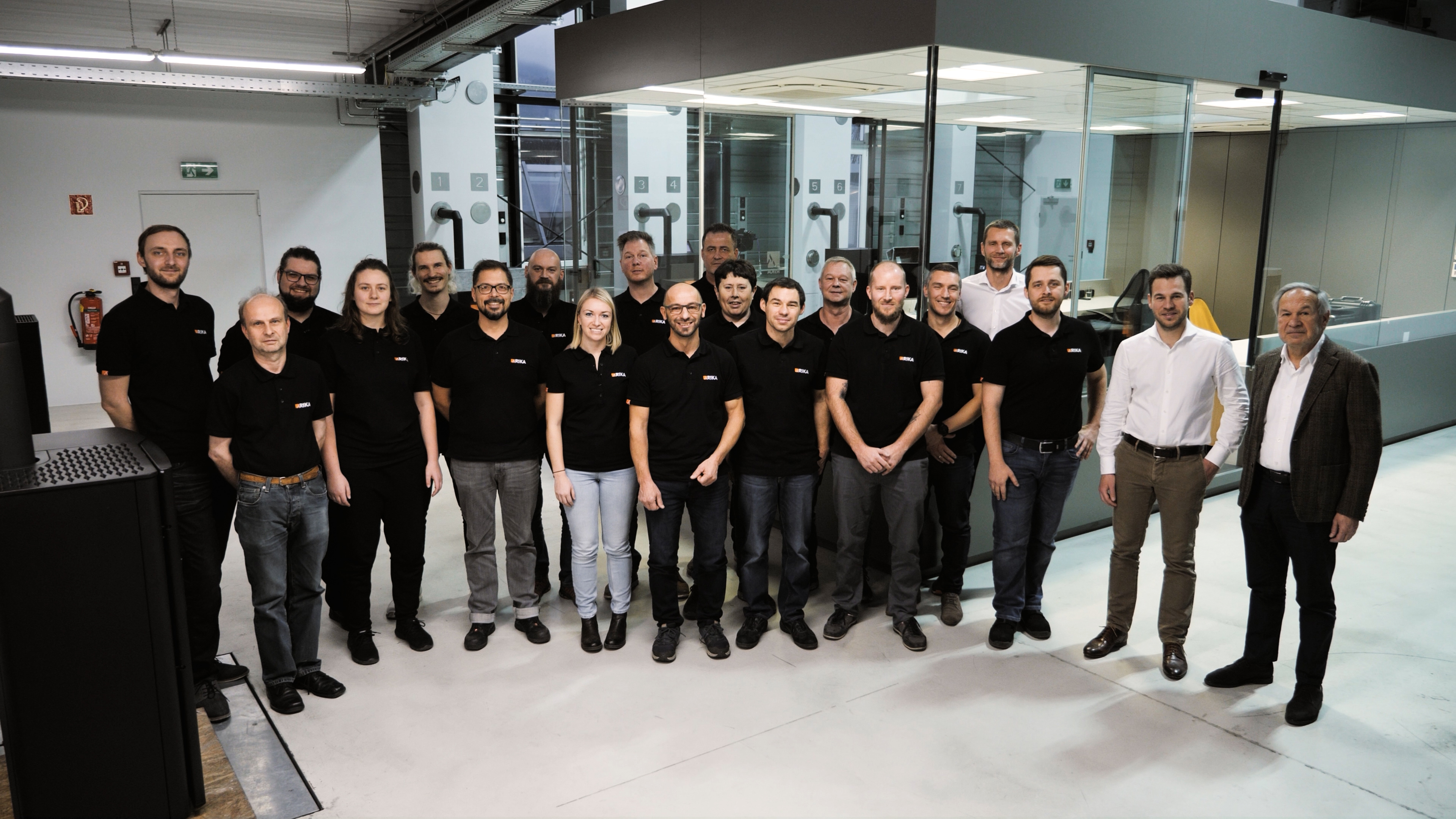
Manuel Kössl, RIKA Technology & Innovation (in the picture fourth from the right): "We are already working on the stoves of tomorrow today. Fire fascinates us, technology is our passion. And that is the special bond we share."
Watch now: RIKA product development